This article explores the various wireless network options available and the limitations that must be addressed in the application process to provide designers with some practical information they need to choose a wireless network for industrial applications. The RKE system for locking and unlocking car doors is a classic example of a simple command and control application. In RKE applications, commands are sent from the remote control key to the car receiver. The door will be locked and unlocked in response to the correct receipt of the order.
This article refers to the address: http://
In theory, receivers of similar models can also accept packets sent from any similar model of the remote control key, but the vehicle will only accept commands from the only matching remote control key. The unique identification code is transmitted from the remote control key to the car, usually using a protocol such as a rolling code generator and secure encryption. As a result, your remote control key cannot unlock your friend's similar car and vice versa, which ensures safety. In the case of the car RKE, the remote key operator can usually hear the locked sound. If you do not hear this "lock" sound, the operator only has to press the button again. In this way, human-computer interaction completes the feedback loop in the RKE example. If you don't hear the door unlocking, just press the button again until you hear it.
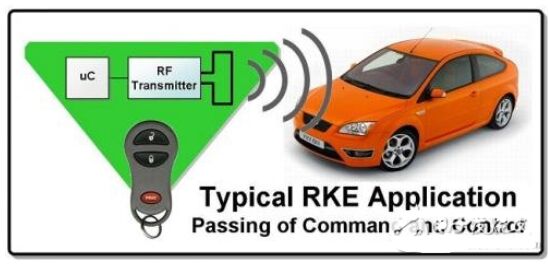
Figure 1. RKE application
Many mission industry applications need to transfer data of command and control types. For example, send a temperature indication of the sensor to the host. The difference between industrial applications and RKE is that the former does not require a person to confirm whether the temperature indication is actually received. The prerequisite for confirming that the data is received is that a two-way network must exist. As the demand for drives, switches, and motors involved in data transmission increases, so does the complexity of the system. Therefore, industrial networks typically do not use a simple one-way RKE network because it is necessary to confirm that the transmitted data is actually delivered. Basically, each node of an industrial wireless solution contains a microcontroller. This type of microcontroller is connected to physical devices such as temperature sensors and drives to read or write data to these devices. At the same time, this microcontroller is also responsible for managing the RF network protocol. The choice of the agreement depends on a number of factors. Transmission range, data rate, power consumption, and complexity of network protocol stacking are all factors that determine which solution is best.
ZigBee has recently received a lot of attention. As a standard network, ZigBee or 802.15.4 is a good choice for many low-power, low-data-rate wireless communications applications in the beginning. But is it really suitable for all applications? The answer is of course not. In some cases, 802.11 WLANs are a seamless match for high data rate communications. Similarly, some applications require longer transmission ranges and longer battery life. In short, the specific architectural reasons determine the type of wireless network required for a particular application.
In wireless networks, an increase in data rate will also drive a corresponding increase in system resources. Taking 802.11 WLAN as an example, the power consumption and code length required to deploy the network determine that these protocols are not suitable for most embedded applications. A typical 802.11 WLAN node requires 1MB of program memory and a more powerful processor to deploy a single function node.
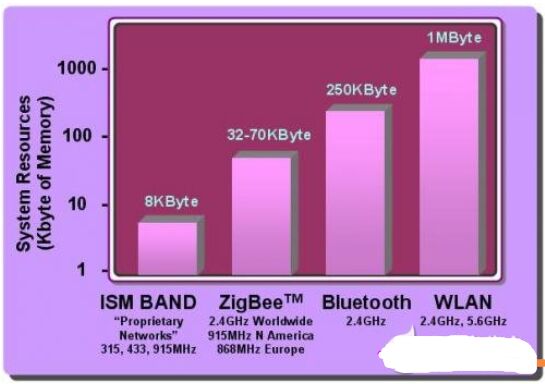
Figure 2. System resources required for different RF networks
Bluetooth is another option that is often mentioned in industrial applications. But the fact that Bluetooth's transmission range (short) and code requirements (slightly larger) and its own point-to-point communication scheme make it excluded from the choice of industrial RF applications. What about private networks? Private networks are networks that operate independently of standard networks. The frequency bands for such networks are typically 915 MHz ISM (Industrial, Scientific, and Medical) and 2.4 GHz. In command and control type applications, bands of 315 MHz or 433 MHz are sometimes used. Local regulatory requirements usually specify the type of frequency that can be used.
As a radio frequency signal transmitted by air, the speed of its power reduction is inversely proportional to the transmission distance and proportional to the frequency. In addition to the path loss in free space, the signal is further attenuated by the blockage of buildings, plants and other objects during transmission. Other factors (such as multipath and signal scatter) can also affect the receiver's decoding of the received RF signal. Other path loss models (for example, the Hata model) also need to consider the ground clearance of the antenna and the loss of urban influence. These models are a more realistic display of path loss. In most applications, the actual path loss value is much higher than the data shown in Figure 3. Interestingly, if the frequency increases, the path loss will also increase. This is one of the reasons why the 2.4GHz system has a smaller transmission range than the equivalent 915MHz or 433MHz system.
A rule of thumb commonly used in RF engineering is that for every 6 dB increase in link budget, the transmission distance will be approximately doubled. Just keep this in mind and you can easily calculate that the 915MHz system has twice the transmission distance of the 2.4GHz system. Similarly, the transmission distance of the 433MHz system is twice that of the 915MHz system. Therefore, systems with lower frequencies can transmit data over longer distances. Data rate is also a key element when choosing frequencies and modulation types for industrial networks. As mentioned earlier, a dedicated network that operates small software stacks at low power is the best choice for applications such as remote temperature monitoring and drive. Designers can customize these packages as expected, greatly simplifying these networks.
1.HI tech integrated design, put Solar Panel,led light,controller and battery all in one box,without any cable, very easy for shipment , installation and maintenance
2.Eco friendly with Solar power supply
3.this design is to put high efficiency monocrystalline silicon solar panel,LED lamps,long life Lithum battery and controller all in one box
4.Different power of the light,meet the different requirements used in the road,house or other sites
5.From 15W up to 100W for LED lamps
Integrated Solar Street Light,Integrated Solar Led Street Light,All In One Solar Led Street Light,Integrated Solar Light
Yangzhou Beyond Solar Energy Co.,Ltd. , https://www.ckbsolar.com